Federal Contracting Compliance for Modular Construction: Avoiding Costly Pitfalls
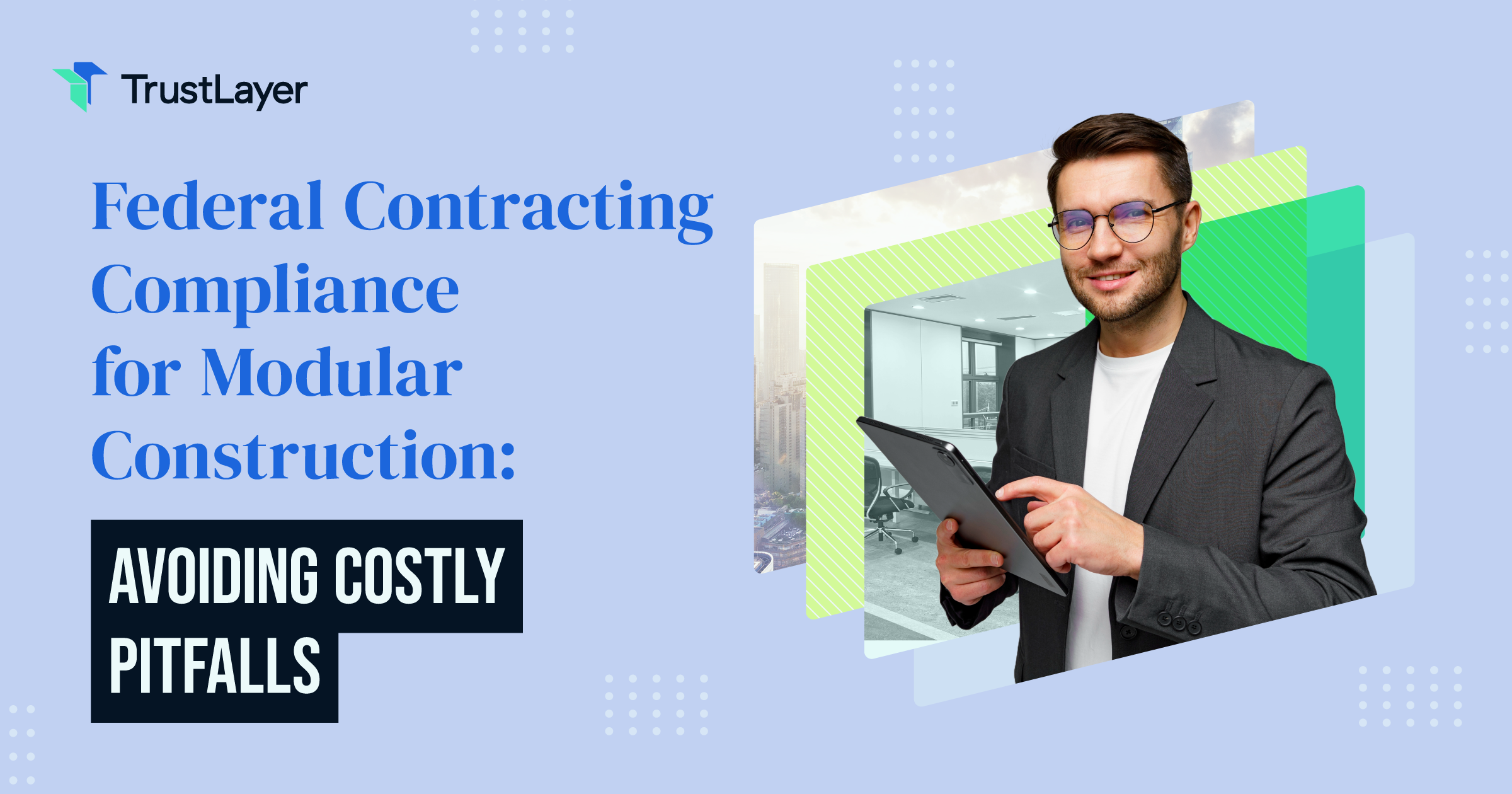
The construction industry has recently witnessed a significant shift towards modular construction methods. This innovative approach, which involves prefabricating building components off-site before transporting them for assembly, has gained traction in federal projects due to its efficiency and cost-effectiveness. Modular construction presents a compelling solution as agencies look for ways to expedite construction timelines and reduce costs.
The increasing demand for modular construction in federal projects
The federal government is increasingly considering modular construction to meet its growing infrastructure needs. With the urgency of modernizing facilities and addressing housing shortages, modular construction offers a rapid response without compromising quality. Constructing buildings in a controlled environment allows for better quality assurance and reduced waste, making it an attractive option for federal contracts. Moreover, modular construction can significantly shorten project timelines, enabling agencies to respond quickly to emergencies or urgent requirements, such as disaster relief housing or temporary facilities for public services.
In addition to speed, the sustainability aspect of modular construction cannot be overlooked. Many federal projects are now mandated to adhere to green building standards, and modular construction inherently supports these goals by minimizing material waste and optimizing energy efficiency. The use of advanced materials and technologies in modular units often results in buildings that are quicker to erect and more environmentally friendly, aligning with the federal government's commitment to reducing its carbon footprint and promoting sustainable practices.
Why federal contracting compliance is a significant hurdle for modular builders
Despite its advantages, modular construction faces significant challenges, particularly in federal contracting compliance. Navigating the complex landscape of regulations can be daunting for modular builders. Compliance with federal guidelines is not just a bureaucratic hurdle but essential for securing contracts and ensuring project success. Understanding these requirements is crucial for avoiding costly pitfalls that could derail projects and harm reputations. Modular builders must often contend with varying standards across different federal agencies, complicating project planning and execution.
The intricacies of federal contracting compliance also extend to the procurement process, where modular builders must demonstrate their capability to meet stringent quality and safety standards. This often involves extensive documentation and rigorous inspections, which can be time-consuming and resource-intensive. As a result, many modular construction firms invest in compliance training and legal expertise to navigate these challenges better, ensuring they remain competitive in a rapidly evolving market. By proactively addressing compliance issues, these builders can secure federal contracts and enhance their overall operational efficiency and reputation within the industry.
Understanding Federal Contracting Compliance for Modular Construction
To thrive in the federal contracting arena, modular builders must grasp the intricacies of federal contracting compliance. This understanding begins with the Federal Acquisition Regulation (FAR), which governs how federal contracts are awarded and managed. Familiarity with FAR helps navigate the complex landscape of federal contracts and positions builders to leverage opportunities that arise from government projects, which often have significant funding and visibility.
The role of FAR compliance in modular project approvals
FAR compliance is a cornerstone of federal contracting. It outlines the rules and procedures contractors must follow to be eligible for federal projects. This means ensuring that modular builders' processes, materials, and labor practices align with FAR stipulations. Failure to comply can result in disqualification from bidding or, worse, termination of existing contracts. Moreover, adherence to FAR can enhance a contractor’s reputation and reliability in the eyes of federal agencies, potentially leading to more contract opportunities in the future. This compliance also encourages a culture of accountability and transparency, which is crucial in maintaining the integrity of federal procurement processes.
How modular construction regulations Impact Contract Eligibility
In addition to FAR, modular builders must also be aware of specific regulations that pertain to modular construction. These regulations can affect everything from the design and engineering of modular units to the methods used for assembly and installation. Understanding these nuances is essential for ensuring that projects meet federal standards and remain eligible for funding and support. For instance, modular construction often requires adherence to specific building codes and safety standards that vary by state or locality. This means that builders must comply with federal regulations and stay informed about regional requirements, which can complicate the bidding process and project execution. Furthermore, as modular construction gains popularity for its efficiency and sustainability, staying ahead of regulatory changes can provide a competitive edge in securing federal contracts.
The Davis-Bacon Act: What Modular Contractors Need to Know
The Davis-Bacon Act is another critical legislation that modular contractors must navigate. This act mandates that workers on federal construction projects be paid prevailing wages, which can vary significantly depending on location and project type. Understanding the nuances of this act is essential for contractors who wish to maintain compliance and uphold fair labor practices, especially in an industry that is rapidly evolving with new technologies and methodologies.
Wage compliance under the Davis-Bacon Act requirements
For modular builders, ensuring compliance with the Davis-Bacon Act involves meticulous attention to wage rates and labor classifications. Contractors must pay their workers according to these prevailing wage rates and maintain accurate records to demonstrate compliance. This can be particularly challenging in modular construction, where labor may be sourced from multiple locations and subcontractors. Additionally, the fluctuating nature of prevailing wage determinations means that contractors must stay informed about any changes that could affect their projects. Utilizing software solutions that track wage rates and automate compliance reporting can be beneficial in managing this complexity.
Common missteps modular builders make and how to avoid them
One common misstep is incorrectly classifying workers, which can lead to underpayment and legal repercussions. Modular contractors should invest in training and resources to ensure that all personnel understand the requirements of the Davis-Bacon Act. Regular audits of payroll practices can also help identify and rectify potential compliance issues before they escalate. Furthermore, contractors must engage in open communication with subcontractors about wage requirements. Establishing clear expectations and providing them with the necessary tools and knowledge can help mitigate risks associated with non-compliance. By fostering a culture of compliance and accountability, modular builders can protect their businesses and contribute to the construction industry's overall integrity.
Prequalifying for Federal Contracts: Key Steps for Modular Contractors
Prequalification is a critical step for modular contractors aiming to secure federal contracts. This process involves demonstrating the ability to meet federal standards and deliver quality work on time and within budget.
The importance of modular contractor prequalification
Prequalification enhances a contractor's credibility and streamlines the bidding process. Federal agencies often prefer to work with prequalified contractors, as it reduces the risk associated with project execution. For modular builders, establishing a solid prequalification record can open doors to more significant opportunities in federal contracting. Furthermore, a well-documented prequalification process can serve as a marketing tool, showcasing a contractor's commitment to quality and compliance, which can be particularly appealing to government agencies looking for reliable partners.
Documentation and insurance requirements for federal projects
Documentation plays a vital role in the prequalification process. Modular contractors must provide detailed information about their business practices, financial stability, and previous project experience. Additionally, securing the necessary insurance coverage is crucial. Federal projects typically require specific insurance policies to protect against potential liabilities, and failure to meet these requirements can result in disqualification. This includes general liability insurance, workers' compensation, and sometimes even specialized coverage, depending on the nature of the project. Moreover, contractors should be prepared to present their safety records and quality assurance processes, as these elements are increasingly scrutinized by federal agencies eager to minimize risks and ensure project success.
In addition to insurance and documentation, modular contractors should also focus on understanding the federal procurement process. Familiarity with the Federal Acquisition Regulation (FAR) can provide insights into the specific requirements and expectations of federal contracts. Engaging with industry associations and attending workshops can further enhance a contractor's knowledge and network, allowing them to stay updated on best practices and emerging trends in federal contracting. By proactively addressing these aspects, modular contractors can significantly bolster their chances of successful prequalification and ultimately secure valuable contracts that contribute to their growth and reputation in the industry.
Reducing Risk and Ensuring Compliance with FAR and Insurance Tracking
Managing compliance and risk is an ongoing challenge for modular contractors. Effective tracking systems are essential with the complexities of federal regulations and insurance requirements. The stakes are exceptionally high in the modular construction industry, where projects often involve multiple stakeholders, each with their compliance obligations. The ability to navigate these complexities safeguards the contractor’s reputation and ensures the smooth progression of projects from inception to completion.
Managing subcontractors and vendors under FAR compliance
For modular builders, managing subcontractors is particularly important. Each subcontractor must also comply with FAR regulations, which can complicate project management. Establishing clear lines of communication and ensuring that all parties understand their compliance obligations can mitigate risks and enhance project outcomes. Regular training sessions and updates on FAR requirements can empower subcontractors to take ownership of their compliance responsibilities. Furthermore, utilizing centralized platforms for documentation can foster transparency and accountability, allowing all parties to track compliance in real time and address any issues as they arise.
The risks of manual federal project insurance tracking
Manual tracking of insurance and compliance documentation can lead to errors and oversights. This increases the risk of non-compliance and can result in costly delays. Implementing automated tracking systems can streamline the process, ensuring all necessary documentation is current and easily accessible. This proactive approach helps contractors maintain compliance and focus on delivering quality projects. Additionally, automated systems can generate alerts for upcoming deadlines, such as insurance renewals or compliance audits, allowing contractors to avoid potential pitfalls. By leveraging technology, modular contractors can enhance operational efficiency and reduce the likelihood of facing penalties or project interruptions due to compliance failures.
How Modular Builders Can Stay Competitive in Federal Contracting
In a competitive landscape, modular builders must find ways to differentiate themselves. Compliance automation and streamlined processes can provide a significant edge.
The competitive advantage of compliance automation
Investing in compliance automation tools can enhance efficiency and reduce the likelihood of errors. Modular contractors can free up valuable resources by automating tracking and reporting processes, allowing teams to focus on core construction activities. This not only improves compliance but also bolsters overall project performance. Furthermore, with the increasing complexity of federal regulations, having a robust compliance automation system in place can help mitigate risks associated with non-compliance, which can lead to costly fines and project delays.
Case studies of modular contractors who streamlined compliance processes
Several modular contractors have successfully implemented compliance automation, improving project outcomes. For instance, companies that adopted integrated compliance management systems reported reduced administrative burdens and enhanced visibility into their compliance status. These success stories testify to the benefits of embracing technology in the modular construction sector. In one notable case, a modular builder cut their project approval times by 30% after integrating a compliance tracking tool, which allowed for real-time updates and notifications. This accelerated their project timelines and improved client satisfaction, as stakeholders were kept informed throughout the construction process.
Moreover, adopting compliance automation has fostered a culture of accountability within these organizations. Teams are now more aware of compliance requirements and are better equipped to meet them, leading to a more proactive approach to risk management. As a result, modular builders are enhancing their operational efficiency and positioning themselves as reliable partners in federal contracting, where adherence to strict regulations is paramount. This shift towards a more technology-driven approach sets a new standard in the industry, encouraging other contractors to follow suit to remain competitive.
Streamlining Federal Contracting Compliance in Modular Construction
Federal contracting compliance for modular construction is complex but essential to securing and executing federal projects. Modular builders can navigate these challenges by understanding the intricacies of FAR compliance, the Davis-Bacon Act, and prequalification processes. Embracing automation and proactive compliance strategies will mitigate risks and enhance competitiveness in the evolving landscape of federal contracting.
As modular construction revolutionizes federal contracting, compliance remains critical in maintaining a competitive edge. TrustLayer is at the forefront of simplifying this process with our best-in-class certificate of insurance (COI) tracker. Designed for the modern risk manager, TrustLayer's platform is trusted by hundreds of thousands of companies for seamless tracking, proof of insurance, and vendor document management. Don't let manual verification slow you down. Embrace the future of risk management with TrustLayer's automated solutions, and join the industry leaders who have already moved beyond outdated practices. Set up a time to talk with our team and discover how we can help you streamline your compliance management and stay ahead in the fast-paced world of federal contracting.